Keep It Moving: What to Consider When Choosing a Conveyor
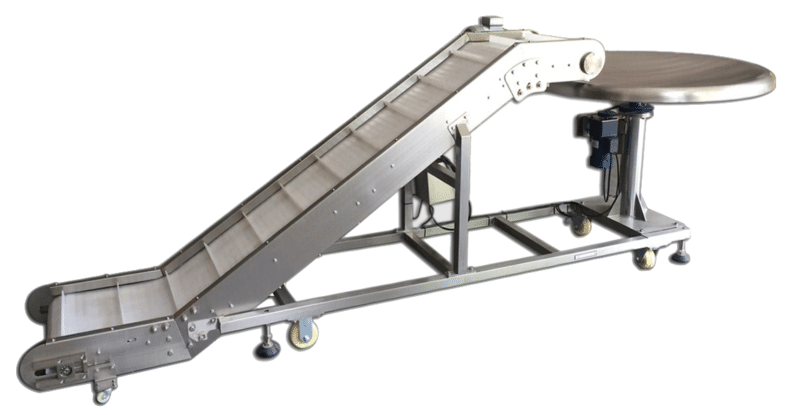
Conveyors are an important part of the commercial packaging process, enabling the consistent movement of products from one stage to the next. While there are several types of conveyors available, packagers should carefully consider their unique requirements when integrating these systems into their operations.
In this article, we’ll explore some of the key questions manufacturers should take into account and describe a few common scenarios in which conveyors can be used to automate the packaging process.
Scenarios for Conveyor Integration in Automated Packaging
Conveyors can be integrated into a packaging system in a variety of ways, depending on the specific requirements of the application. Below are a few common cases in which conveyors can be used to automate the packaging process.
Bottling Line: A bottling line often includes several stages, including filling, capping, labeling and packaging. Conveyors can be used to move bottles or cartons between each stage, effectively automating the entire process.
Food Packaging Line: In food packaging, it’s essential to maintain a hygienic environment to prevent contamination. Conveyors designed for use in food packaging are often made from materials that are easy to clean and can withstand high-pressure washdowns.
E-commerce Fulfillment: In e-commerce, the packaging process typically involves picking and packing individual items, placing them in shipping boxes and labeling them for shipment. Conveyors can be used to move products from the pick-and-pack area to the shipping area, allowing for fast and efficient fulfillment.
Pharmaceuticals: Conveyor systems are also suited to pharmaceutical packaging, where products need to be transported and sorted according to varying specifications.
Confectionery & Sweets: Vacuum conveyors for granules or powders, incline conveyors for items such as donuts and other models can assist sweets manufacturers in transporting products for packaging.
Automotive: In the automotive industry, conveyors can shift heavy parts and components between manufacturing lines.
Questions to Consider When Implementing Conveyors in a System
Through proper planning and integration, conveyors can significantly improve productivity and efficiency. With a reduced need for manual handling, conveyors bring down labor costs, help to minimize the risk of product damage or contamination and limit bottlenecks in the packaging process. Additionally, conveyors are highly customizable, with various configurations available to suit different products and packaging needs.
Before integrating conveyors into a packaging environment, manufacturers should consider several questions to ensure the system is optimized for their specific needs.
What type of conveyor is best suited for my product and packaging process?
Different conveyors are designed to handle different products, and manufacturers should choose the system best suited for their particular application. For example, bucket elevators can be ideal for transporting bulk materials or small items, while vacuum conveyors are perfect for free-flowing granules and powders. Incline elevators may be more appropriate for moving heavy items vertically.
What are my space constraints?
Once the appropriate conveyor has been selected, manufacturers should consider the flow and path of the packaging process within a space. Some packaging environments may have limited space, requiring manufacturers to choose a conveyor system that can accommodate these limitations. BPI offers conveyors of varying heights and can change out the feet of conveyors to add or reduce height, if needed.
What is my required production rate?
Manufacturers must choose a conveyor system that can keep up with their required output rate to ensure that the production line operates efficiently.
What are my safety requirements?
Conveyors can pose a safety risk to operators if not properly installed and maintained. Manufacturers should consider their safety requirements when selecting a provider and implementing a conveyor system. BPI ensures customers are properly trained on the operation of all equipment and provides manuals that detail safety measures.
What level of automation do I need?
Manufacturers should determine how much automation they need for their packaging process and choose a conveyor system that aligns with this level of automation. Some operations may only need a bucket conveyor to feed product into a scale while other production lines may require transition conveyors as well as pack-off conveyors.
How BPI Can Help
From heavy-lifting bucket conveyors to motion conveyors that can adapt to complex part geometries, BPI Equipment provides a perfect solution for all automated packaging needs.
Our team of experts are dedicated to guiding you on the options best fit for your operation, whether you need long-term production throughput or quick, pick-and-pack workflows.
Capable of integrating with a variety of baggers, scales, bottlers, cartoning machines and more, we offer industry-leading, stainless steel systems with precision controls, such as incline elevator conveyors, sloped conveyors, vacuum conveyors and comprehensive pack-off systems. Our staff will work with you to define the most cost-effective platform for your application which offers the appropriate capacity, space requirements, production speed and more.
Have a question about your automated packaging process? Are you unsure where to begin in searching for a new or refurbished machine? BPI Equipment staff are here to help. Contact us today to schedule a consultation and take your first step toward improved operations!