Keep It Clean: Maintaining Stainless-Steel Machinery for Automated Packaging
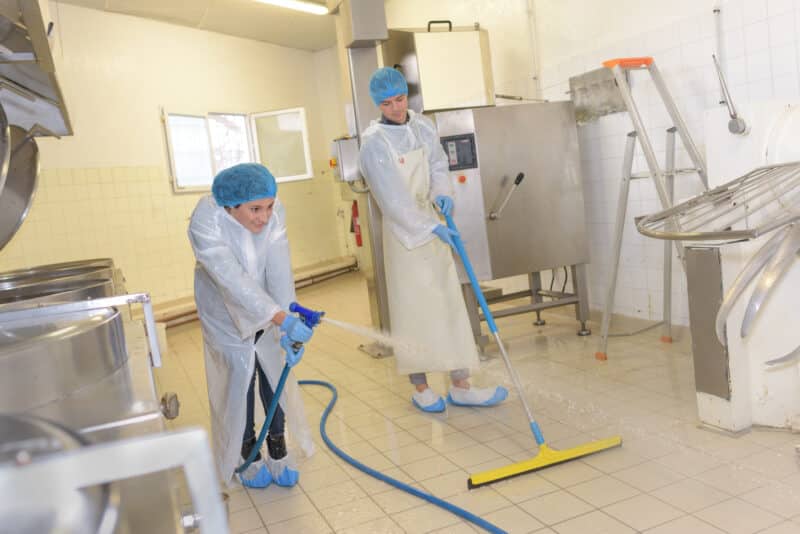
When running an automated commercial packaging operation, it’s essential to keep your machinery well maintained to ensure optimal performance and safety. This applies particularly to stainless steel machinery, which requires regular cleaning and maintenance in order to remain in peak condition.
In this article, we will discuss best practices for keeping your stainless-steel machinery clean, lubricated and well maintained, as well as the importance of weekly maintenance reviews and how washdown capabilities can boost your operation’s efficiency.
Daily Cleaning
A key part of maintaining stainless-steel machinery is making sure it is regularly cleaned. Some processes require more frequent cleaning than others. For example, machines that are used in food production require more frequent cleaning than those used in non-food applications, but all require consistent cleaning to prevent dirt and grime from building up on the machine surfaces.
Daily wiping down with a damp cloth or towel should be sufficient for most scenarios; however, industrial-grade detergents may be necessary for more heavily soiled machines. Be sure to avoid harsh abrasives and corrosive chemicals on stainless-steel surfaces as these can damage them irreparably.
This daily cleaning will help prevent damage from occurring on the metal due to long-term exposure to moisture and other contaminants. Additionally, daily cleaning will make it easier to spot potential problems with the equipment before they become more serious issues.
Proper Lubrication Following Cleaning
Once the machine has been appropriately cleaned, lubrication should be applied immediately afterward. This helps protect the internal parts of the machine against corrosion and wear caused by friction between moving surfaces.
Depending on the application, specific types of lubricant may be recommended by the manufacturer of your machine; however, a general-purpose lubricant such as silicone grease or oil should suffice in most cases. Be sure to apply evenly over all movable parts and in available grease fittings to ensure maximum effectiveness.
Remember: never attempt to lubricate any electrical components as doing so could cause significant damage or a fire hazard.
Weekly Maintenance Reviews
Proactive habits limit headaches. Inspect your packaging machinery periodically for any signs of deterioration or damage such as loose nuts/bolts or worn out parts/belts. This helps identify any potential issues before they become more serious problems down the road.
Although daily cleaning and checking should suffice for most components, once a week it’s good practice to take a closer look at all areas of the machine — internal and external — and make certain everything is working properly before continuing with production operations. If anything seems off during your inspection, don’t hesitate to contact a professional technician who can diagnose and repair the issue.
Washdown Equipment
For industries where sanitation standards must be met (such as food packaging or pharmaceuticals), washdown-capable machines are often chosen instead of non-washdown machines due to their ability to resist water intrusion at high pressure levels (measured by IP ratings). They’re also popular among cannabis producers who typically experience high levels of residual buildup and may require deep cleaning of equipment due to contamination from pests.
For high-volume operations that must stay clean between each run, washdown equipment may be the right fit for quickly removing potential contaminants from both inside and outside the machine.The benefits of washdown equipment are obvious:
• Reduced downtime due to fewer cleanings required throughout the day
• Improved product quality by reducing bacteria growth
• Reduced wear on components due to decrease in build-up and grime over time
• Extended life expectancy due to increased care given during regular maintenance intervals
However, there are certain instances where washdown equipment may not be ideal: if there’s limited workspace available within an operation, as many washdowns tend take up quite a bit of space, or if products vary greatly between cycles, thus requiring different types of cleaning processes.
When purchasing new equipment, it’s imperative you understand if your machinery is wash down-duty or not. If you’re unsure, BPI staff can help you determine the machine’s IP rating and capabilities.
Ingress Protection Ratings
The Ingress Protection rating (or simply IP rating) is an international standard used by manufacturers measure the sealing effectiveness of electrical enclosures against intruding objects, dust particles and water. The IP rating consists of two numbers — one representing solid particle protection levels (ranging from 1–6) and another representing liquid ingress protection levels (ranging from 1–9).
For example; an IP65 rated enclosure means that particles ranging from 0–1mm in size cannot penetrate through the enclosure nor can jets from any direction at pressure rate 6 bar, whereas an IP67-rated enclosure resists pressure jets up 8 bars. It’s important that you select a machine based on its respective IP rating depending on how much protection you need against both solid particle and liquid ingress.
Make sure you also select enclosures according these standards when using sensitive electronic components such as touch screens or wiring systems.
How BPI Can Help
With the wide range of stainless-steel, automated packaging machines available — both washdown-capable and non-washdown — BPI has the perfect solution for numerous commercial industries. Even better, BPI’s repair technicians are available for on-site service of your system should any issue arise. If you’re seeking automated packaging solutions or advice on how to keep your machinery at optimal levels of performance, reach out to BPI today!