The Biggest Mistakes Businesses Make When Automating Their Packaging Processes
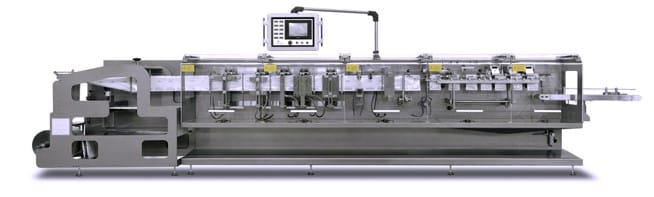
If your business isn’t already using some form of automated packaging, chances are you’re at least considering it. After all, with the ever-growing demand for faster turnaround times and higher outputs, manual packaging simply can’t keep up.
When it comes to automated packaging solutions, there’s no one-size-fits-all answer. The right choice for your business depends on a variety of factors, including the type of products you manufacture, your production volume and your budget. Yet time and time again, we see businesses make the same mistakes when trying to determine how to approach automating their packaging processes.
Before making the jump to automation, it’s important to avoid making some of the common mistakes that can cause inefficiencies and added costs down the line. Here are some of the biggest mistakes manufacturers make when automating their packaging processes — and how to avoid them.
Not Conducting a Thorough Needs Assessment
Before investing in any type of packaging automation, it’s crucial to conduct a thorough needs assessment. This will help you determine exactly what type of automated system would best suit your needs — and just as importantly, what type of system would be unnecessary and overkill. BPI’s team of experts can assist you in conducting a needs assessment and determining which type of automation would be right for your business.
Take a close look at your current process. What are its strengths and weaknesses? Are there any bottlenecks that could be eliminated with automation? Once you’ve assessed your current process, you’ll have a better idea of what needs to be improved and how automation can help.
Not Having a Clear Goal in Mind
When you’re considering automation, it’s important to have a clear goal in mind. What exactly do you hope to achieve by automating your packaging process? Is your goal to increase efficiency? Reduce costs? Improve safety? Once you know what your goal is, you can start to look for packaging solutions that will help you achieve it.
Not Considering ROI
Another mistake businesses make is not considering return on investment (ROI) when determining if automation is right for their business. While there are many benefits to automating your packaging process — including increased efficiency and decreased labor costs — you need to make sure that the upfront investment will pay off in the long run. One way to do this is by calculating the cost per minute of downtime for your existing packaging process and comparing it to the cost of an automated system.
How long will it take for the solution to pay for itself? Will it save you money in the long run? Will it help you achieve your goal?
Falling Victim to ‘Scope Creep’
It’s not uncommon for “scope creep” to occur during a business’s implementation of their automated packaging solution. Scope creep refers to the tendency for the requirements of a project to grow beyond its original plans. This usually happens because stakeholders don’t properly communicate their needs or because project goals change over time. To avoid scope creep, it’s important to have a clear understanding of what you want from your automated packaging solution from the outset.
Underestimating the Importance of Change Management
Automating your packaging process is a big change for any business — and like any other big change, it needs to be managed properly to be successful. That’s why it’s important to have a dedicated team in place to manage the transition from manual to automated packaging. This team should be responsible for conducting training, implementing best practices and overseeing the day-to-day operations of the new system.
Overlooking the Interaction Between Departments
When automating your packaging process, it’s important to take into account how different departments within your organization will interact with the new system. For example, will customer service need to be trained on how to use the new system? Will accounting need to learn how to track inventory levels? Addressing these questions upfront will help ensure a smooth transition for everyone involved.
Forgetting About Maintenance and Upkeep
Once your automated packaging system is up and running, it’s important to maintain it properly to prevent costly downtime and disruptions in production. Creating a preventive maintenance plan — and sticking to it — is crucial for keeping your system running smoothly. BPI offers on-site service contracts that provide our team of experts with regular access to your equipment so we can identify and fix potential issues before they become major problems.
Not Monitoring Performance
Perhaps one of the most important — yet often overlooked — aspects of automating your packaging process is monitoring performance on an ongoing basis. This includes tracking things like cycle time, output levels, reject rates and more. By monitoring performance regularly, you can make adjustments as needed to ensure that your automated system is running as efficiently as possible.
Not Seeking Expert Input
Finally, don’t forget to seek expert input when evaluating packaging solutions. Making the switch from manual to automated packaging can be a big undertaking — but if done correctly, it can have a major impact on your business’s bottom line.
The staff at BPI has years of experience helping businesses find the right packaging solutions for their needs. We can help you assess your current process, evaluate different options and choose the right solution for your business. Contact us today!